月刊自動認識2013年01月号
RFIDを利用した検査品のリアルタイムロケーション管理
月刊自動認識2013年1月号
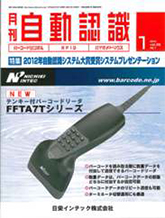
月刊自動認識2013年1月号
見える化を実現するにはデータの収集が欠かせない。しかしながらデータの収集には少なからず現場での入力作業などが増えるため、なかなか正確・大量なデータを収集することは難しい。RFIDを利用すればこの煩雑な入力作業を軽減し、かつ大量なデータを収集することが可能となる。今回のシステムは株式会社ニコン相模原工場様で導入された検査品のリアルタイムロケーション管理であり、それを利用した見える化の取り組みである。
見える化を可能にするパッケージ
当社では、製造現場における見える化を実現するパッケージとしてRFIDリアルタイムロケーション管理パッケージ『MANICAトレイサー』を開発した。
MANICAトレイサーはRFIDを利用し、工場内で製造される多数の製品および製造に携わる作業員の所在を管理する。システムの概要を図1に示す。図1は3つのエリアで製品が検知されている様子を示す。工場内の各所に据え置き型のRFIDリーダライタ(写真1)を設置し、管理したいエリアごとにアンテナを据え付ける。製品自体もしくは製品に付属の現品票などにRFタグを取り付ける。作業員にはRFタグが貼付されたIDカードを携帯していただく。そして、各エリアのアンテナでRFタグの進入と退出を検知し、製品や作業員の所在を管理する。RFIDリーダライタはネットワークに接続され、アンテナからの情報はサーバで集中管理される。
基本的な仕組みは上記だけなので非常に簡単だ。サーバに蓄積されたデータは専用アプリやWebブラウザで閲覧することができる(図2)。
![]() 図1 概要イメージ |
|
![]() 写真1 エイリアンテクノロジー製UHF帯据置型リーダライタ |
|
![]() 図2 履歴検索画面 |
システムの特長
RFIDを予備品管理に利用することによって、以下のような利点がある。
リアルタイムな所在の把握 |
|
---|---|
所在の把握は見える化により得られる効果の最も基本的なものだが、これだけでも非常に効果的だ。例えばある製造番号の製品が今どこにあるのかを把握したいことはよくあると考えられる。現在の進捗を確認したい場合や、特に急いで納品をしなければならないような製品の状況把握、また使用部品等に欠陥が見つかり、すぐに製造ラインから外したい製品を探す場合などである。このような場合通常は基幹システムの情報から大まかな作業場所を推測し、実際に現場に出て探すという作業になる。この探すという作業が実は時間がかかり、大きな労力となっている場合が少なくない。この時間を短縮することだけでも大きな効果が得られる。 |
|
停滞品の把握 |
|
一般的にある工程での作業は、先に届いたものを先に処理することが望ましい。いわゆる先入れ先出しであるが、これが徹底されていないと、その工程で製品が停滞してしまうという問題が発生する。また、工程間の運搬中に仮置き場に置いたまま放置されていたりすることもあるだろう。このような状況はいずれもリードタイムを伸ばす原因となり排除する必要がある。システムでは、ある一定期間特定のエリアに製品が居続けた場合や、一定期間システム内のいずれのアンテナでも検知しなかった場合などに停滞品とみなしてアラートが出る仕組みとなっている。この機能により、停滞品をなくすことができ、リードタイムの短縮が可能となる。 |
|
エリアごとの現在作業量の把握 |
|
各作業エリアにアンテナが設置してあれば、各エリアに現在どのくらいの製品があるのかを知ることができる。各エリアの製品数を比較すれば、溜まっているエリアもあるだろうし、空いているエリアもあるだろう。このような状況を把握することでリアルタイムに調整を行うことが可能となる。 |
|
作業員の配置状況 |
|
製品の現在数量だけでなく、作業者が多い場合は作業者数の把握も可能だ。比較的空いているエリアに必要以上に作業者がいる場合などにはすぐに対応できる。 |
|
詳細な進捗の把握 |
|
作業工程が厳密に定められており、かつ作業エリアと工程が結び付けられるような場合には製品の動きから現在の進捗を把握することが可能だ。例えばA,B,C,Dの4つの工程からなる製品があるとして、アンテナでA,Bと検知していれば現在の進捗は4つのうちの2つ目であるとわかる。基幹システムがある場合には通常作業工程の始まりと終わりにバーコードなどで入力させる場合が多いが、作業が細かい場合などは何度も入力する必要があり、手間がかかるので大まかな工程で入力するといった省略がなされることが多い。しかしRFIDであればエリアに運び込めば検知されるので入力の手間は必要ないため、エリア単位で入、出を把握するこができる。 |
|
作業工数の正確な算出 |
|
データが蓄積されていくと、それを元に様々な有用なデータを得ることが可能だ。作業エリアの入を作業開始、作業エリアからの出を作業終了と定めると、作業工数が実際にはどの程度かかっているのかを知ることができる。作業工数は多くの場合は作業者のヒアリングから作業にはこの程度かかるとの判断がなされるが、それには実際の開始までの作業時間、終了後の作業時間、エリアに保管されている時間などが考慮されていないなどの理由で正確でない。これらを客観的に正確なデータへと修正することが可能になる。 |
|
納期の正確な見積 |
|
作業工数の正確な算出ができると、今度は完成までどのくらいかかるかの見積が可能になる。これは正確な納期回答と結びつき、サービスレベルの向上となる。 |
|
スケジューリングへの活用 |
|
正確な進捗の把握、作業工数の見積ができるようになると、スケジューリングへの活用も可能だ。例えば翌日の各工程ごとの作業量を把握してしまえば、翌日作業員をどの程度配置すれば効率的かなどの判断が可能になる。 |
導入事例~株式会社ニコン相模原製作所様
相模原製作所様では、半導体露光装置、液晶露光装置など高精度硝子材料、光学部品の開発・製造を行っており、その製造品目は多品種小ロットとなっている。精密なものであるため、工程の各所において検査が実施される。検査もたくさんの種類があり、大掛かりな機械を使用するものもあるために工場内の1箇所ではなく複数の場所にて検査が行われている。そのため、多品種小ロットの製造品が工場の各所に散在することとなり、さまざまな問題が存在していた。その中でも主な問題点は以下の2つである。
特定の検査品の所在の詳細がわからない。 |
|
---|---|
基幹システムへバーコードを利用した入力は行っているため、おおまかな場所の予測は可能であるが、実際どの部屋のどこにあるのかまで知ることはできない。そのため、納期を急がなければならなくなった等の理由で検査品を見つける必要が生じた場合、その検査品を探し回る作業が発生している。 |
|
リードタイムにバラつきがある。 |
|
検査工程においては、先入れ先出しが基本であるが、何らかの理由によりそうならなかったなどの理由で、同じような品目の製品でもリードタイムが他のものと比べて大きいものが存在する。そういう製品が数個あっただけでも、リードタイムの平均を採ると底上げになり全体として悪い数値となってしまうし、正確でない。 |
これらの問題を解決するため、RFIDを利用した見える化のパッケージ「MANICAトレイサー」をカスタマイズして導入いただいた。
RFタグの取り付け
検査品の所在を管理するためには、検査品にRFタグを取り付けなければならない。しかしながら、検査品は加工・洗浄されるので直接貼付することはできない。各検査品には基幹システムから現品票が発行され、検査品と同じトレイに入れられている(図3)。今回はこの現品票に着目し、現品票にRFタグを取り付けることにした。また現品票に直接貼ってしまうとランニングコストが上がってしまうため、RFタグを取り付けたクリアフォルダを用意し、それに現品票を入れる運用によってRFタグをリサイクルして使用できるようにした。クリアフォルダへ貼り付けるRFタグは読み落としを少なくするために2枚ずつ貼るようにし、クリアフォルダは重ねてトレイに入れられることがあるため、RFタグが重なって読み取りができなくならないように各フォルダに貼るRFタグの位置をそれぞれ異なるようにすることで、フォルダが重なってもRFタグが重ならないようにする工夫も行った(図4)。
![]() 図3 検査品と現品票 |
|
![]() 図4 RFタグ付クリアフォルダ |
アンテナの取り付け
詳しい検査品の所在を把握するためには、RFタグを読み取るリーダ側のアンテナの配置が重要だ。アンテナが少なければ大まかな把握しかできないが、多くするためにはアンテナの費用や設置費用がかかってしまうため、適度なバランスが必要となる。出入口が限られているような場所では、出入口のみに設置することでアンテナの数を減らすことができる。詳細を把握するためにアンテナを多く取り付けた場合は、アンテナ間の干渉があるために電波シールドなどの利用の検討が必要となる場合がある。
大画面にリアルタイムな情報表示
MANICAトレイサーにより収集された情報はWebブラウザを利用して検索や参照を行うことができる。ニコン様では独自にカスタマイズを行い、大画面モニタに現状がリアルタイムに表示されるようになっている。特に工程別に停滞状況を示す棒グラフはどの工程で停滞品が多く発生しているのかが一目でわかるようになっている(図5)。
![]() 図5 大画面表示の構成 |
導入による効果
システムの導入により、当初問題とされていた点は改善することができた。
特定の検査品の所在の詳細がわからない。 |
|
---|---|
特定の検査品の所在を知りたい場合はWebブラウザを使用して検索すればよく、今どこにあるのか、直近にどこにいたのかがすぐに参照できるため探索する手間はほとんど無くなった。 |
|
リードタイムにバラつきがある。 |
|
大画面モニタに表示される停滞品の情報により停滞品を減少させることができたため、リードタイムの大幅な改善ができた。実際のデータとして2012年1月から4月のデータを示す。1月から4月の検査品で、特に動きの多かった製品上位5種を抽出し、1月から3月のリードタイムの平均を100とした場合の4月のリードタイム値を計算した。これにより4種の品目において20%から40%の削減ができていることがわかる(図6)。 |
|
![]() 図6 リードタイムの改善 |
今回のシステム導入においては主に上記のような効果が得られたが、その他にも様々な効果が得られた。見える化によって物の動きの詳細が掴めるようになったことで想定と異なる動きをしていたりしていることが多く見つかった。今までなぜ停滞していたのか不明だったものが、だんだんと明らかになっていった。これらを1つ1つ改善していくことで全体として大幅な工数削減が可能となった。
このように見える化により現状を把握することは管理面から効果があるというに留まらず、具体的な改善の糸口をたくさん得ることができ、費用対効果としても大きなものが得られるのだ。