月刊自動認識2012年04月号
製造業におけるRFIDを利用した究極の見える化
月刊自動認識2012年4月号
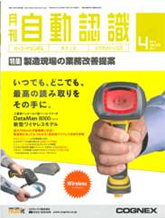
月刊自動認識2012年4月号
見える化は近年においては経営に関する重要な要素であり、様々な手法、定義が存在するが、本稿では製造現場における見える化について考える。製造現場における見える化の目的は在庫の削減、納期の短縮にある。見える化によってボトルネックとなっている工程を見つけだしたり、製造物のもの探しなど単純だが時間のかかっている作業を省くことができるようになる。
これを実現するためにすべての製造物が今どこにどういう状態にあるのかを把握すること、およびすべての製造物が出荷されるまでの間にどのような経路を辿りどのように時間をかけられたのかを把握することが必要となる。製造物が少ない場合は手作業で把握することも難しくはないが、何百、何千となってくると細かい動きの把握はほぼ不可能になる。そこでRFIDを活用し、自動認識でこれらを把握することに取り組んでみたのでご紹介したい。
見える化を可能にするパッケージ
当社では、製造現場における見える化を実現するパッケージとしてRFIDリアルタイムロケーション管理パッケージ『MANICAトレイサー』を開発した。
MANICAトレイサーはRFIDを利用し、工場内で製造される多数の製品および製造に携わる作業員の所在を管理する。システムの概要を図1に示す。図1は3つのエリアで製品が検知されている様子を示す。
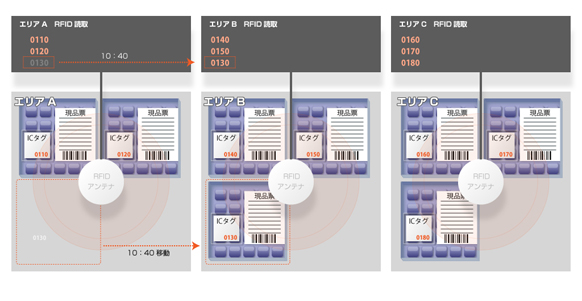
図1 概要イメージ
工場内の各所に据え置き型のRFIDリーダライタ(写真1)を設置し、管理したいエリアごとにアンテナを据え付ける。製品自体もしくは製品に付属の現品票などにRFタグを取り付ける。作業員にはRFタグが貼付されたIDカードを携帯していただく。そして、各エリアのアンテナでRFタグの進入と退出を検知し、製品や作業員の所在を管理する。RFIDリーダライタはネットワークに接続され、アンテナからの情報はサーバで集中管理される。
基本的な仕組みは上記だけなので非常に簡単だ。サーバに蓄積されたデータは専用アプリやWebブラウザで閲覧することができる(図2)。
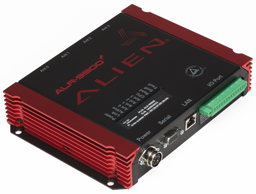
写真1 エイリアンテクノロジー製UHF帯
据置型リーダライタ
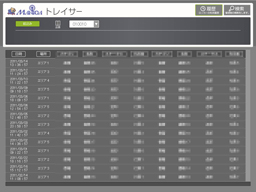
図2 履歴検索画面
導入の効果
実際に導入を行った事例から、どのような効果が見られたのかをご紹介したい。
1.リアルタイムな所在の把握 |
|
---|---|
所在の把握は見える化により得られる効果の最も基本的なものだが、これだけでも非常に効果的だ。例えばある製造番号の製品が今どこにあるのかを把握したいことはよくあると考えられる。現在の進捗を確認したい場合や、特に急いで納品をしなければならないような製品の状況把握、また使用部品等に欠陥が見つかり、すぐに製造ラインから外したい製品を探す場合などである。このような場合通常は基幹システムの情報から大まかな作業場所を推測し、実際に現場に出て探すという作業になる。この探すという作業が実は時間がかかり、大きな労力となっている場合が少なくない。 |
|
2.停滞品の把握 |
|
一般的にある工程での作業は、先に届いたものを先に処理することが望ましい。いわゆる先入れ先出しであるが、これが徹底されていないと、その工程で製品が停滞してしまうという問題が発生する。また、工程間の運搬中に仮置き場に置いたまま放置されていたりすることもあるだろう。このような状況はいずれもリードタイムを伸ばす原因となり排除する必要がある。システムでは、ある一定期間特定のエリアに製品が居続けた場合や、一定期間システム内のいずれのアンテナでも検知しなかった場合などに停滞品とみなしてアラートが出る仕組みとなっている。この機能により、停滞品をなくすことができ、リードタイムの短縮ができた(図3)。 |
![]() 図3 停滞数の表示例 |
3.エリアごとの現在作業量の把握 |
|
各作業エリアにアンテナが設置してあれば、各エリアに現在どのくらいの製品があるのかを知ることができる。各エリアの製品数を比較すれば、溜まっているエリアもあるだろうし、空いているエリアもあるだろう。このような状況を把握することでリアルタイムに調整を行うことが可能となる。 | |
4.作業員の配置状況 |
|
製品の現在数量だけでなく、作業者が多い場合は作業者数の把握も可能だ。比較的空いているエリアに必要以上に作業者がいる場合などにはすぐに対応できる。 | |
5.詳細な進捗の把握 |
|
作業工程が厳密に定められており、かつ作業エリアと工程が結び付けられるような場合には製品の動きから現在の進捗を把握することが可能だ。例えばA,B,C,Dの4つの工程からなる製品があるとして、アンテナでA,Bと検知していれば現在の進捗は4つのうちの2つ目であるとわかる。基幹システムがある場合には通常作業工程の始まりと終わりにバーコードなどで入力させる場合が多いが、作業が細かい場合などは何度も入力する必要があり、手間がかかるので大まかな工程で入力するといった省略がなされることが多い。しかしRFIDであればエリアに運び込めば検知されるので入力の手間は必要ないため、エリア単位で入、出を把握するこができる。 | |
6.作業工数の正確な算出 |
|
データが蓄積されていくと、それを元に様々な有用なデータを得ることが可能だ。作業エリアの入を作業開始、作業エリアからの出を作業終了と定めると、作業工数が実際にはどの程度かかっているのかを知ることができる。作業工数は多くの場合は作業者のヒアリングから作業にはこの程度かかるとの判断がなされるが、それには実際の開始までの作業時間、終了後の作業時間、エリアに保管されている時間などが考慮されていないなどの理由で正確でない。これらを客観的に正確なデータへと修正することが可能になる。 | |
7.納期の正確な見積 |
|
作業工数の正確な算出ができると、今度は完成までどのくらいかかるかの見積が可能になる。これは正確な納期回答と結びつき、サービスレベルの向上となる。 | |
8.スケジューリングへの活用 |
|
正確な進捗の把握、作業工数の見積ができるようになると、スケジューリングへの活用も可能だ。例えば翌日の各工程ごとの作業量を把握してしまえば、翌日作業員をどの程度配置すれば効率的かなどの判断が可能になる。 |
おわりに
MANICAトレイサーは仕組みは非常に単純であり、単にアンテナを多数設置して読み取っているだけだ。これだけなのだが、得られる効果は絶大だ。アンテナを多数設置するということで費用がかかることは事実だが、それに見合うROIを発揮する。また導入は意外にスムーズにできる点も魅力的だ。自動で読取されるので入力の手間もなく、運用を変える必要はない。さらに基幹システムとの連携もほとんどないので、導入にあたり基幹システムを改修する必要もない。
RFIDのシステムというとどうしても一括読取に注目しがちである。100%の読取でないと使えない場合も多い。しかし本システムではアンテナは各所に設置してあり、あるRFタグが各所のアンテナに一度も読まれずに工程を終了することはまずありえない。このようなRFIDの使い方は非常に有効であり、RFIDならではの使い方と言えるのではないだろうか。