月刊自動認識2011年11月号
製造工場内でのRFIDシステム活用事例
月刊自動認識2011年11月号
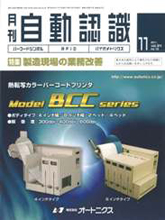
月刊自動認識2011年11月号
RFIDを利用したシステムは物流の分野では活用ケースが増えてきており、特にアパレル関連での活用が目立ってきているが、製造業においても利用シーンは増加してきている。工場でのRFIDの利用においては工場内で完結したシステムとして利用できるので、物流のように大きな活用はできないが導入のしやすさという点では有利である。当社では製造工場においてRFIDならではのシステムを導入した実績があるので、これらのシステムをいくつか紹介したい。
予備部品在庫管理システム
製造工場においては、工場で使用している機械の故障に備えて機械部品の予備部品を在庫していることが多い。たくさんある機械のうち1つでも停止すると、それが生産停止など大きな損害につながる可能性もあるため、機械の故障が発生した場合にはすぐに交換または修理する必要がある。しかしながら工場で使用する機械の部品というものは汎用品であることが少なく、すぐに注文して買えるというものが無いものが多いためどうしても予備として工場内にストックしておく必要がある。ストックする場合にはいくつストックするかという問題も発生する。大量にストックしても無駄であるし、いざ使用するときにストックが無くなってしまっていては致命的な問題である。常に適正な数がストックされるように管理しなければならない。
しかし予備部品は本来の生産業務に必要なものではないのでその管理用のシステムを予算として計上することは難しく、どうしても安易で手軽な台帳などを利用した管理方法になってしまう。ストックされている予備部品のうち何を使用したのかを台帳に記録しておき、ストックが少なくなったものに関しては発注をかけておくような運用である。この運用にも問題がある。
予備部品が必要なときは通常急いでおり、すぐにでも予備部品を運ばなくてはならないために台帳記入を後回しにし、結局忘れてしまうケースが多く発生してしまう。そうすると発注のタイミングを逃してしまい、いざ使用したいときに実はストックが無かったというような事になりかねない。
このような問題を解消するためにRFIDを利用した管理システムを導入いただいた。RFIDを利用した理由は台帳記入忘れをなくすため、予備部品を保管している保管室の出入口にRFIDゲートを設け、台帳記入などを行うこと無しに通過することでストック数の増減を管理するためである。運用イメージは以下の通り。
1.RFタグの登録 |
|
---|---|
予備部品に取り付けるRFタグをシステムに登録する。
登録は専用のPCで行う。予備部品は金属製のものが多いため、簡易な金属対応がなされたRFタグを利用した。
|
|
2.予備部品の入庫 |
|
登録したRFタグを予備部品に取り付け、保管室に持っていく。保管室の出入口にあるゲートでRFタグが読取られ(図1)、自動的にシステム上のストック数が加算される。
|
![]() 図1 RFタグを貼った予備部品を保管室へ運び込む |
3.予備部品の出庫 |
|
予備部品が必要になったときには保管室から必要な予備部品を持ち出す。その際に出入口にあるゲートでRFタグが読取られ、自動的にシステム上のストック数が減算される。 |
|
4.予備部品の発注 |
|
ストック数があらかじめ決められた数量を下回った状態で一定の期間が過ぎた場合に発注依頼のメールが送信される。予備部品は持ち出されたあと、必要なかった、物が違ったなどの理由で再び保管室に戻されることがあるため、決められた数量を下回った瞬間に発注指示が出るような仕組みにはしていない。
|
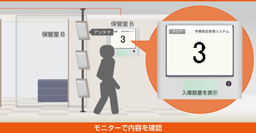
図6 BizICA概要図
RFIDを使用することで予備部品を持ってゲートを通過するだけで読取が行われる。RFIDを利用しない場合には何かに読取らせる、記入するなどの行為が発生してしまうため、この点においてRFIDならではの利用方法となっている。RFIDの弱点である読取り漏れを防ぐための対策としてゲートの近くにモニターを設置し、通過した予備部品の数が通過時に表示され、きちんと読取られているかどうかを確認できるようになっている(図2)。また作業者にもRFタグを所持してもらい、誰がいつ何を何個持って出た(入った)のかが履歴として残るようにもなっている。このシステムにより予備部品のストック管理が非常に楽に行われている。
問題点としては、RFタグの登録という作業が増えることであるが、登録作業は予備部品が必要な緊急時に行うような作業ではなく、通常業務時に行えばよいので大きな問題とはならなかった。
製品所在管理システム
次にに少し大規模な例としてある製造業企業様においての導入事例を紹介する。
導入したのはパッケージソフトウェアの『MANICAトレイサー』で、このシステムでは工場内の各所に据置型のRFIDリーダライタを設置し、工場内で生産する多数の製品の場所をトレースすることができる。
導入された企業様は工場で製品を製造しており、各製品は検査、加工、組立等様々な工程を経て出荷される。
基本的に受注生産のため、オーダーを受けてからの生産となる。
その際に重要となるのが納期であり、どのくらいで出荷可能なのか、また現状はどうなのかを正確に把握することが求められる。
しかしながら生産している製品の数が数千点と大変多く、各工程も各所に点在しているため正確に把握することは困難であった。
『MANICAトレイサー』は以下の機能を持っている。
1.製品の場所を監視、記録する機能 |
|
---|---|
製品自体もしくは製品に付属の現品票などにRFタグを取り付け、据置型のリーダを各所に配置してサーバで集中管理することにより、各製品がどこにあるのか、どのように移動しているのかを記録していく(写真1、図3)。記録された情報は、ブラウザを利用して工場内のどこからでも確認することができる(図4)。 |
![]() 写真1 エイリアンテクノロジー製UHF帯据置リーダライタ |
![]() 図3 概要イメージ |
![]() 図4 履歴検索画面 |
2.アラート機能 |
|
あらかじめ設定を行っておくことで、例えば製品が一定の期間動きが見られない場合などにアラートを出すことができる(図5)。アラートはその他にも特定のステータスの製品が特定のエリアに入った場合などにも出すことができる。 |
![]() 図5 アラート表示 |
3.探索機能 |
|
工場内すべてに据置型リーダを設置することは難しいため、どうしてもRFタグを検知できないエリアに製品が存在することがある。その場合には高出力のハンディリーダを利用して、探知機のように製品を探すことができる。製品のRFタグに反応して音が鳴り出し、近づくと音が変わるのでどこにあるのかをすばやく探すことが可能となる。 |
通常正確なトレースを可能にするためには情報を記録するために何かに読取らせる、入力するといった作業が発生してしまう。しかしRFIDを利用することでそういった作業をしなくても自動的にデータが記録されるのでこれもRFIDならではの利用方法である。
このシステムにより製品のトレースが可能となり、納期回答や問合せの際に正確な情報を提供できるようになった。また、各工程でのリードタイムを正確に測れるようになり、ボトルネックを把握し、設備予算申請時の適正な根拠としての情報提供が可能となった。
さらには各工程の作業量予測が可能となり、作業員の適切な配分や手配ができるようになった。
おわりに
今回紹介した事例ではどちらもRFIDの特徴を利用したシステムになっている。通常業務の中で自動で読取らせ、記録するシステムである。もちろん読取は100%ではないので確認などのステップは必要ではあるが、読取らせる、入力するなどの手間に比べれば大変楽に運用が可能となる。これからもこのような活用は増えていくと考えられる。当社でもさらに導入実績を増やし、面白い活用事例を紹介させていただきたい。