月刊自動認識2016年12月号
製造業におけるRFIDを利用した梱包確認
月刊自動認識2016年12月号
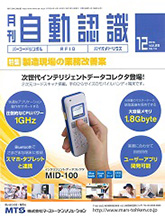
月刊自動認識2016年12月号
近年、製造業では、国内で製造した部品を輸出し、海外の工場で組み立てるなど、グローバル化が進んでいる。グローバル化により、部品を確実に組立工場へ供給する必要がある。部品の輸送は、運送会社へ依頼するが、梱包は製造会社で行う事が多い。
X社では、外注会社も含め、国内で製造した各種の部品を、複数の海外の組立工場へ輸出している。また海外の他社へも部品を輸出している。それらの部品は、国内のX社の工場で梱包している。
今回は、X社の梱包部門に導入した梱包確認システムを紹介したい。
梱包作業の手順とシステム導入前の状況
まず、部品をロット単位でポリ袋へ入れ、部品番号や個数などを印刷したラベルを貼り付ける。次に部品が入ったポリ袋を段ボール箱(内箱)に梱包する。この時、内箱にもポリ袋と同じラベルを貼る。ラベルはポリ袋用と内箱用を別シートで印刷している。複数のポリ袋を内箱へ梱包した場合、その枚数のラベルが内箱に貼られる。
なお、複数種類の部品を1つの内箱にまとめる事もあれば、1種類の部品を複数の内箱へ分ける事もある。最後に、出荷票の部品一覧と、内箱に貼られたラベルを確認しながら、内箱を木箱の中へ入れて梱包する。
システム導入前は、第1図のようになっていた。
![]() 第1図 システム導入前 |
<問題点>
ポリ袋に貼られたラベルの部品番号や個数を目視で確認しながら内箱へ梱包しているため、誤読による入れ間違いが発生する可能性がある。
また、ポリ袋用と内箱用を別々のラベルシートに印刷しているため、貼り間違える可能性もある。
同様に、内箱を木箱へ梱包する時も目視で確認するので、入れ間違える可能性があり、梱包した後は、中身を確認する事ができない。各工程で、作業者と管理者が二重チェックしているが、繁忙期は1名の場合もあり、誤出荷が発生しやすい。
誤出荷の頻度は低いが、日本へ返品するための輸送費や税関手続きの時間を考えると、1回の誤出荷による損失は大きい
システム導入により誤出荷を防ぐ事ができないか相談を受け、RFIDを利用した方法を提案した。
RFIDタグラベルへの変更
木箱は厚さ3cmの合板と木製の梁でできている。また、部品は金属であるが、内箱に梱包する際に梱包材を詰めるため、内箱との間に隙間ができる。
以上の状況から、内箱へRFIDタグを貼り、木箱に梱包した後は、中のタグを読み取って確認する事にした。タグには、システム用に追加した管理番号(出荷番号を基に採番)をエンコードする。
また、部品を入れたポリ袋を内箱に梱包する時に確認するため、ポリ袋に貼るラベルに管理番号や部品番号等のQRコードを印刷する。
RFIDタグラベルは、スリットで2つに分かれるレイアウトとした(第2図)。
![]() 第2図 RFIDタグラベルのレイアウト |
以降、タグが有る方をタグ、タグが無い方をラベルと呼ぶ。
さらに、出荷票に出荷番号のバーコードを追加した。
このように、目視による梱包確認でなく、RFIDタグやQRコード、バーコードを利用して確認する事にした。
システム導入により、第3図のように変更した。
![]() 第3図 システム導入後 |
なお、作業現場ではWi-Fiが使用できないため、出荷指示データや確認結果データはハンディリーダー内に保存する。リーダーに保存されたデータは、事務所にて、クレードル経由でデータをシステムへ取り込む。
1. 内箱への梱包と確認 |
|
---|---|
梱包作業の手順に従い、システム導入後の状況を説明する。 まず、出荷指示データを元に、RFIDタグラベルを発行し、部品をポリ袋に入れラベルを貼る。 また、その部品を梱包する内箱にはタグを貼る(第4図)。なお、木箱に梱包した時、タグが重ならない様に、タグを貼る内箱の面や位置を決めておく必要がある。 |
|
![]() |
|
次に、ハンディリーダーで出荷票のバーコードを読み取り、梱包する出荷番号を指定する。ポリ袋を内箱へ梱包する時、ラベルのQRコードを読み取る。指定した出荷番号とは異なる場合、エラーとする。内箱への梱包が終わると、内箱に貼られたタグを読み取り、ポリ袋の管理番号と照合する(第5図)。 |
|
![]() 第5図 内箱への梱包と確認 |
|
正しく内箱へ梱包された事を確認した後、確認結果データをシステムへ取り込む。 |
|
2. 木箱への梱包と確認 |
|
タグが貼られた内箱を木箱へ梱包する。なお、作業の都合により、梱包後に確認する事とする。内箱の場合と同様、ハンディリーダーで出荷票のバーコードを読み取り、出荷番号を指定する。 次に、木箱の外側から、梱包された内箱のタグを読み取り、管理番号を照合する(第6図)。正しく木箱へ梱包された事を確認した後、確認結果データをシステムへ取り込む。 |
|
![]() 第6図 木箱への梱包と確認 |
システム導入の効果
システムを導入してから半年ほど経過したが、今のところ誤出荷は発生していない
1年後、あるいは数年後に、導入前後の誤出荷の件数を比較する事により、具体的な数字で効果が確認できる。今後も経過を見守っていくつもりである。
また、導入前は、出荷先ごとにチェックシートを作成し、印刷していた。内箱や木箱への梱包時、担当者がチェックシートに捺印して確認済みとしていた。さらに、チェックシートを参照し、進捗状況を確認していた。
導入後は、梱包確認データをシステムに保存し、PCより参照できるので、複数の出荷先でも、容易に進捗状況を確認できるようになった。
ハンディリーダーによる確認作業の手間が増えたが、進捗管理の効率がアップするなど、全体の仕事量は、あまり変わらない。
おわりに
当社では、製造現場における見える化を実現するパッケージとしてRFIDリアルタイムロケーション管理パッケージ『MANICAトレイサー』を開発した。工場内で製造される多数の製品にタグを付け、据置型リーダーでタグを読み取る事により、所在を管理するパッケージである。
今回は、梱包確認システムのみの導入であるが、もしも、MANICAトレイサーのタグを利用して梱包確認を行った場合、出荷まで見える化を実現できる。つまり、MANICAトレイサーの所在の管理は、梱包作業の現場までであるが、梱包から出荷までも現品確認できるようになる。